Case overview
A Manufacturing company leading in the production of electronical industrial components, tackled inefficiencies in their quality control processes. The company faced challenges with prolonged inspection times and high costs associated with traditional methods of lot acceptance sampling. The goal of the project was to introduce a statistical system for lot acceptance sampling to optimize quality control, reduce inspection times, and lower costs.
Problem
Company has found that verifying the quality of each individual component is costly in terms of time and resources. Additionally, full inspection of each item slows down the production process, negatively impacting the company’s ability to meet customer delivery deadlines. Consequently, the company faced the challenge of finding an efficient and effective way to ensure the quality of their products without compromising productivity.
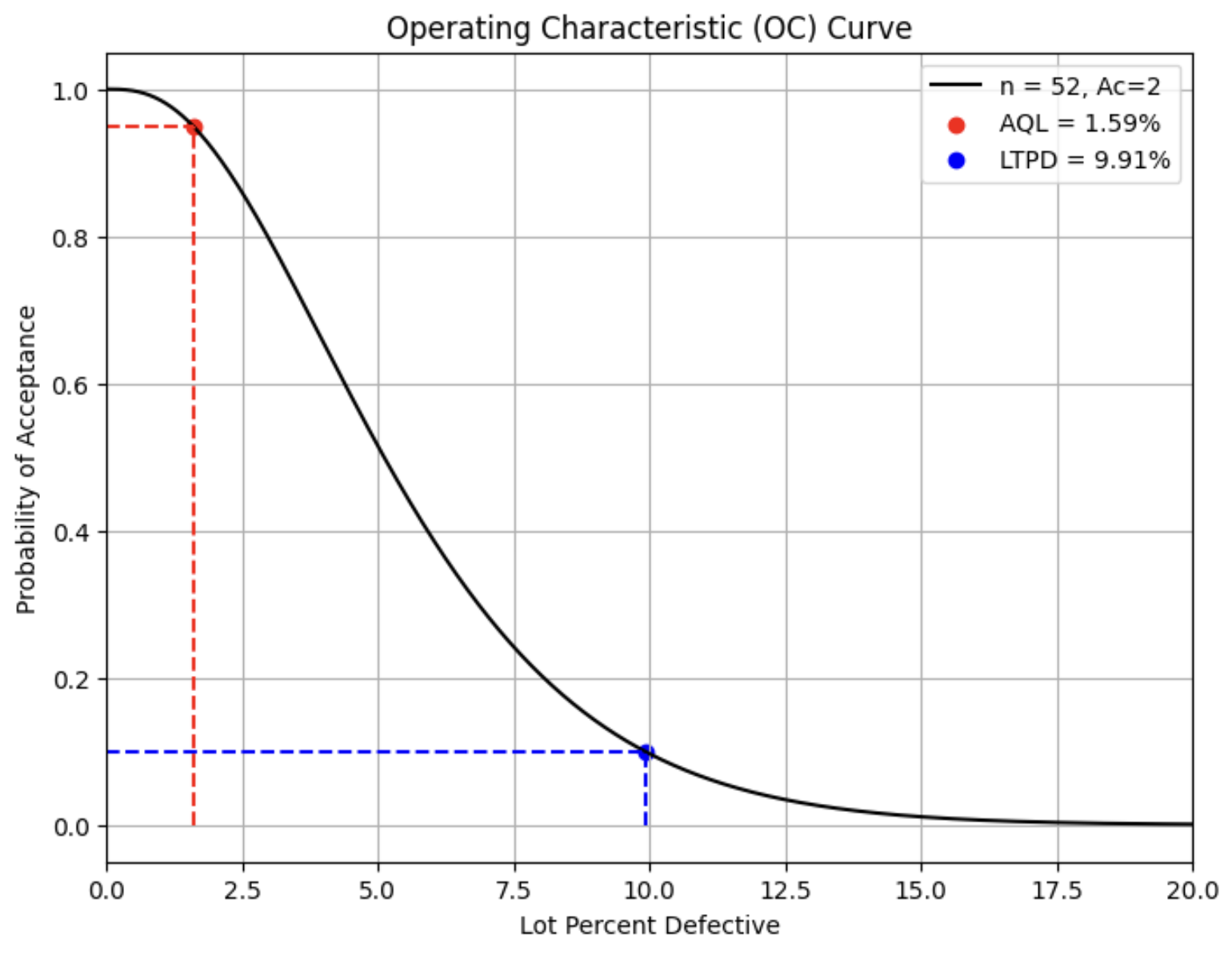
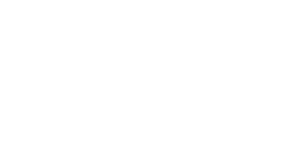
Solution
The proposed solution introduced a statistical system for lot acceptance sampling based on sampling plans. This system allowed for faster and more accurate inspections by focusing on representative samples rather than the entire lot. The statistical approach reduced variability in results and enabled more informed and timely decision-making.
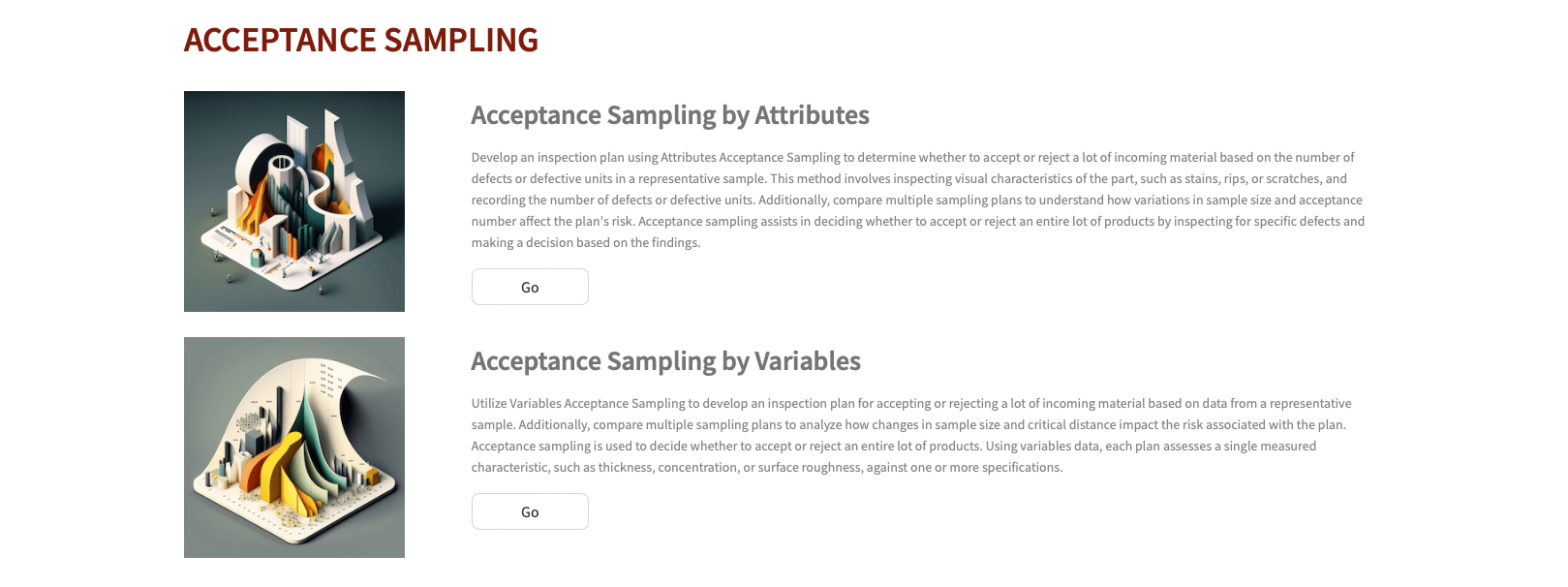
Implementation
The implementation of the statistical system was carried out through the following phases:
- Preliminary Analysis: Collection of historical data on lots and existing quality control processes.
- Definition of Sampling Plans: Development of specific statistical sampling plans for different types of lots and materials.
- Staff Training: Training of personnel involved in the new control processes, ensuring a thorough understanding of statistical methods.
- Pilot Testing: Pilot implementation of the system on a sample of lots to verify effectiveness and make necessary improvements.
- Full Deployment: Full-scale implementation of the system throughout the company, with continuous monitoring and process improvement.
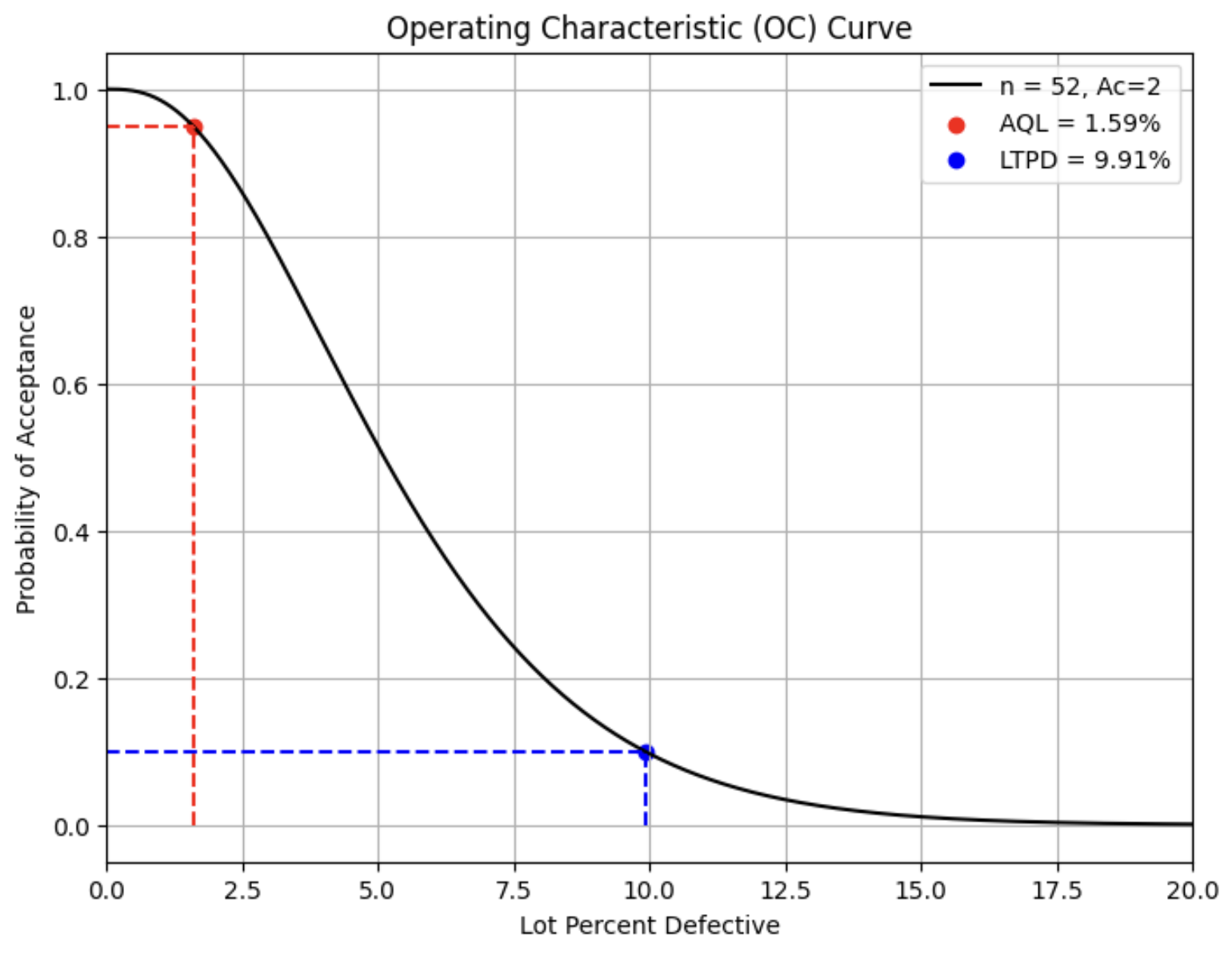
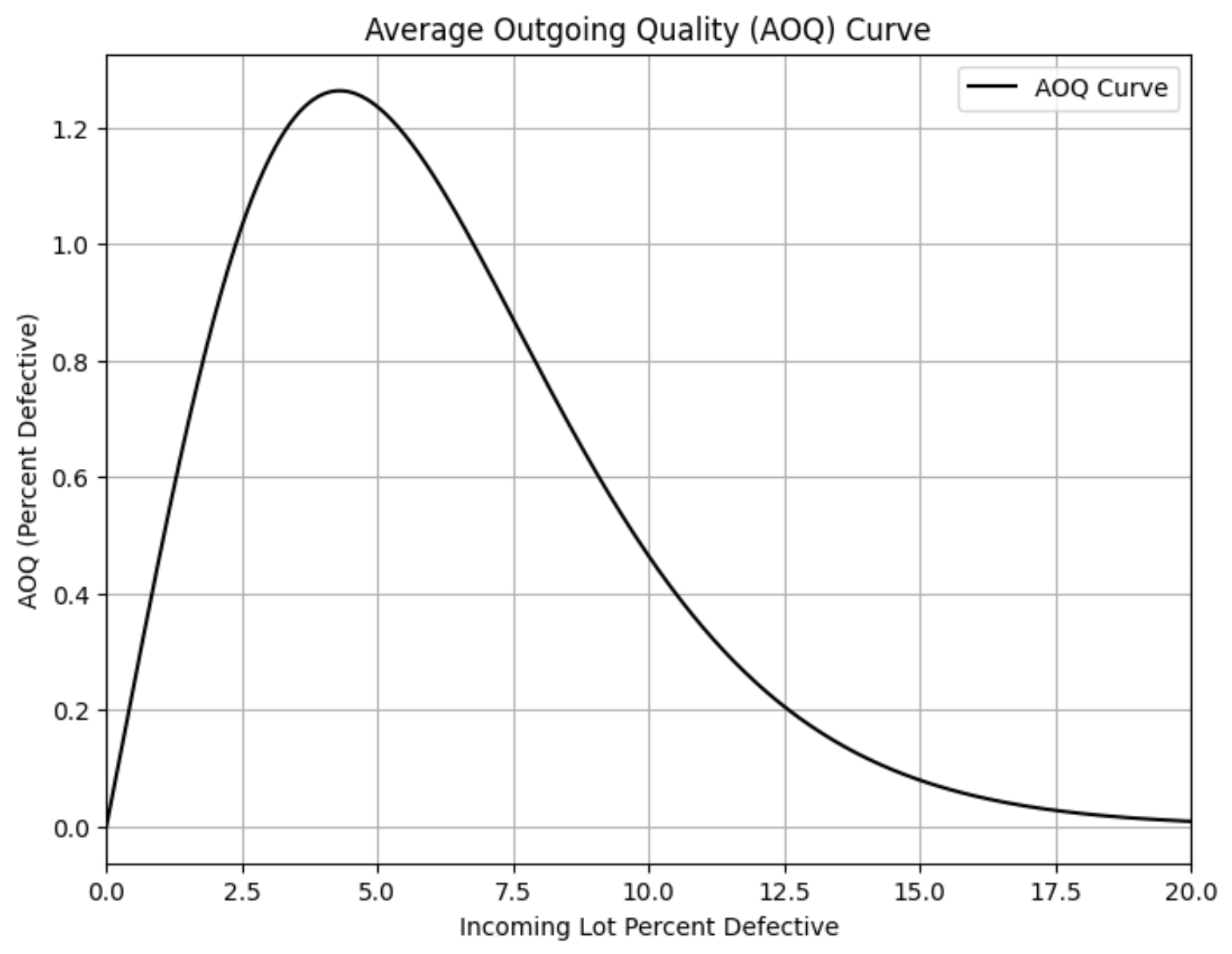
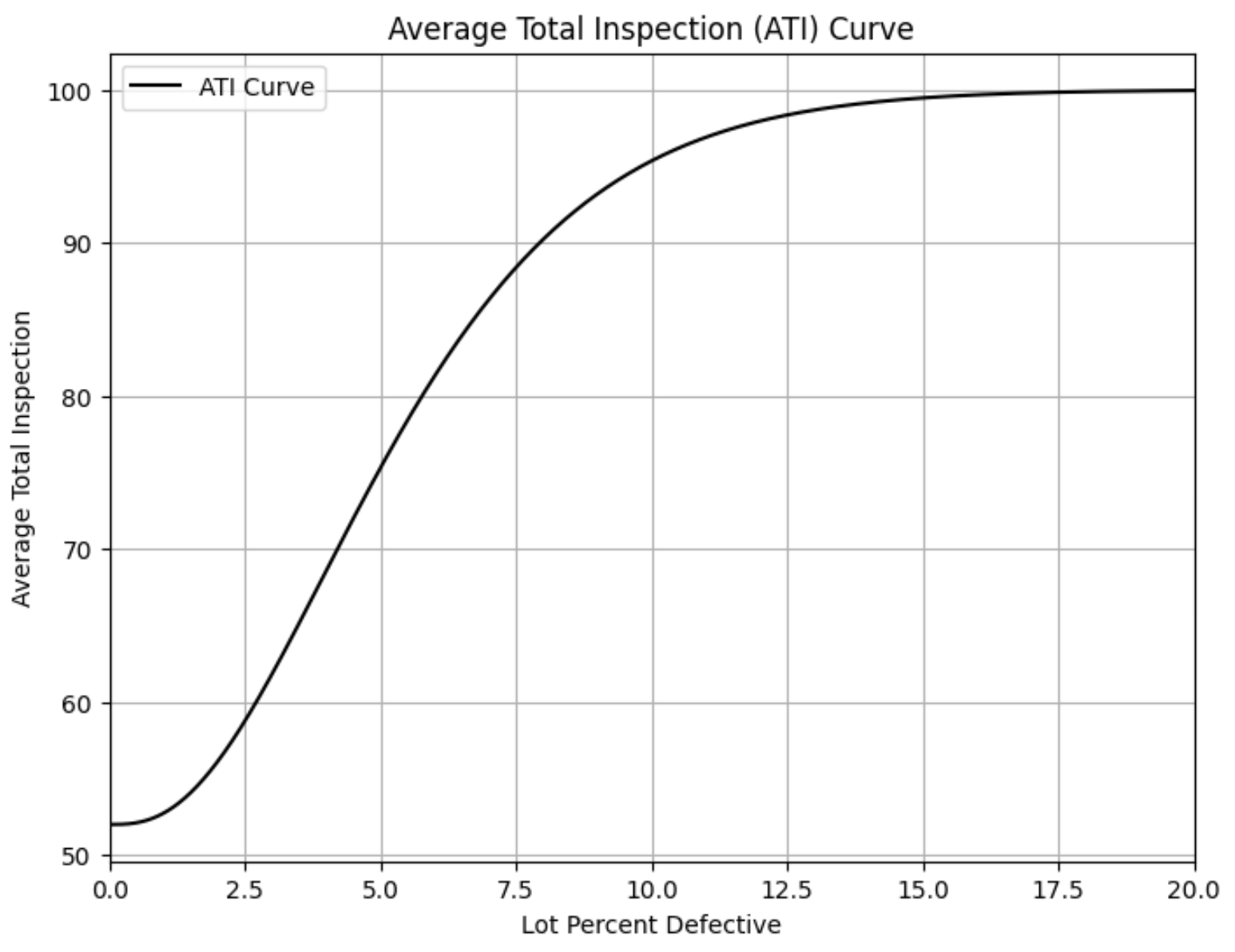
Benefits
The introduction of the statistical system for lot acceptance sampling brought numerous benefits to the company, including:
- Reduction in Inspection Times: Inspection times reduced by 50%, accelerating the production process.
- Cost Reduction: Decrease in operational costs related to quality control due to reduced resource usage.
- Quality Improvement: More accurate and timely decisions reduced product defect rates.
- Increased Competitiveness: Optimization of processes made the company more competitive in the market, improving customer satisfaction.
- Operational Efficiency: Greater efficiency in lot management, with a significant reduction in waste and rework.
In conclusion, the implementation of acceptance sampling allowed Company to optimize its production process while maintaining high quality standards and maximizing operational efficiency.