Case overview
In the ever-evolving realm of industrial processes, maintaining peak efficiency and quality remains a persistent challenge. To address this, our project ventures into the development of a groundbreaking tool for Statistical Process Control (SPC). This undertaking seamlessly integrates the strengths of R, Python, Minitab, and Spotfire to forge a comprehensive solution that not only monitors and analyzes processes but also delivers actionable insights for improvement.
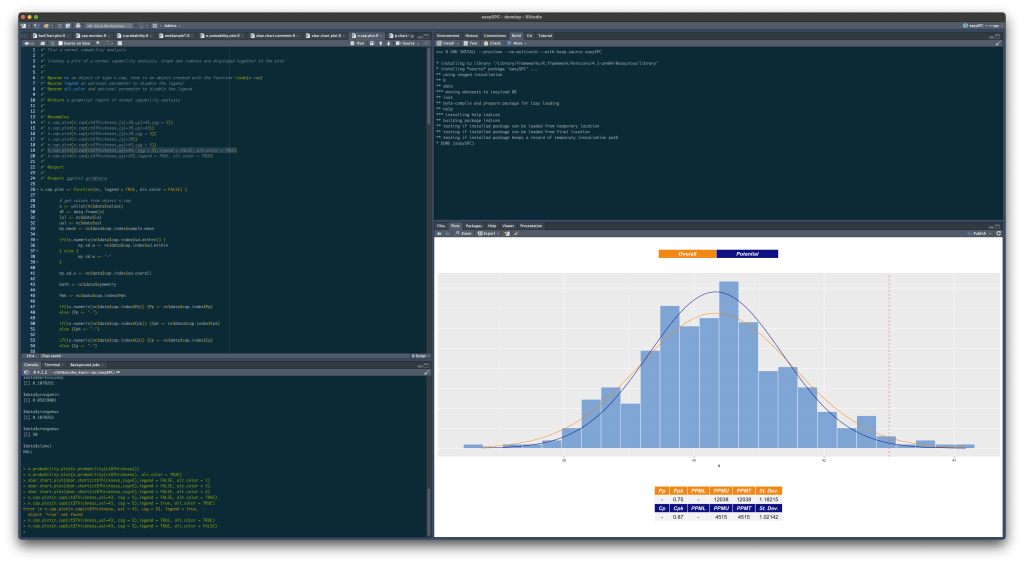
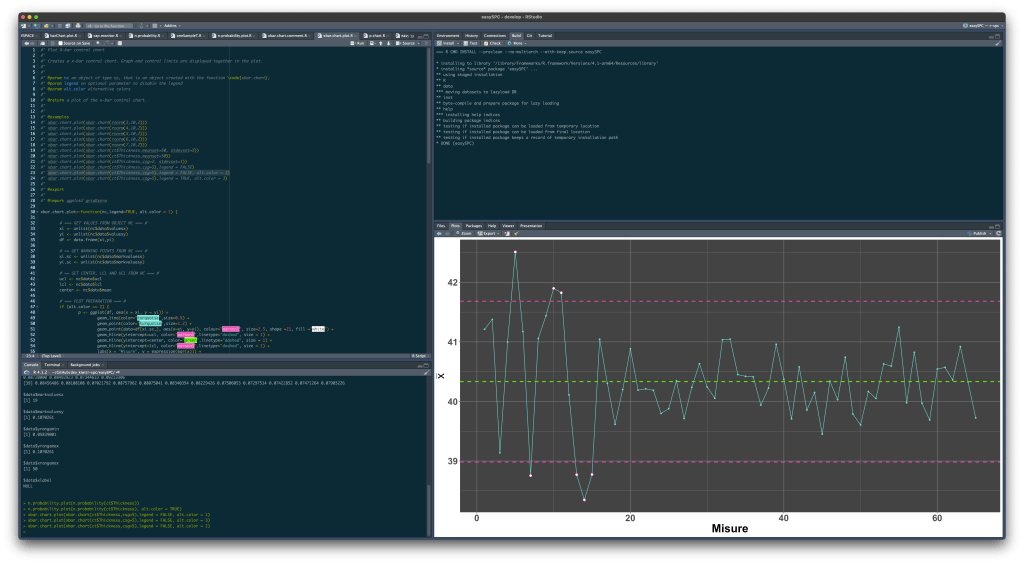
The R package
At the heart of this endeavor lies โeasySPC,โ a versatile R package designed to equip data analysts, quality control professionals, and engineers with a comprehensive arsenal of SPC analysis functions. This encompassing package seamlessly interweaves various statistical methods to evaluate normality, assess temporal stability through control charts, and gauge key performance indicators (KPIs) such as PPK, CPK, CP, and PP.
Key Features:
- Normality Test
- Control Chats
- Process Capability
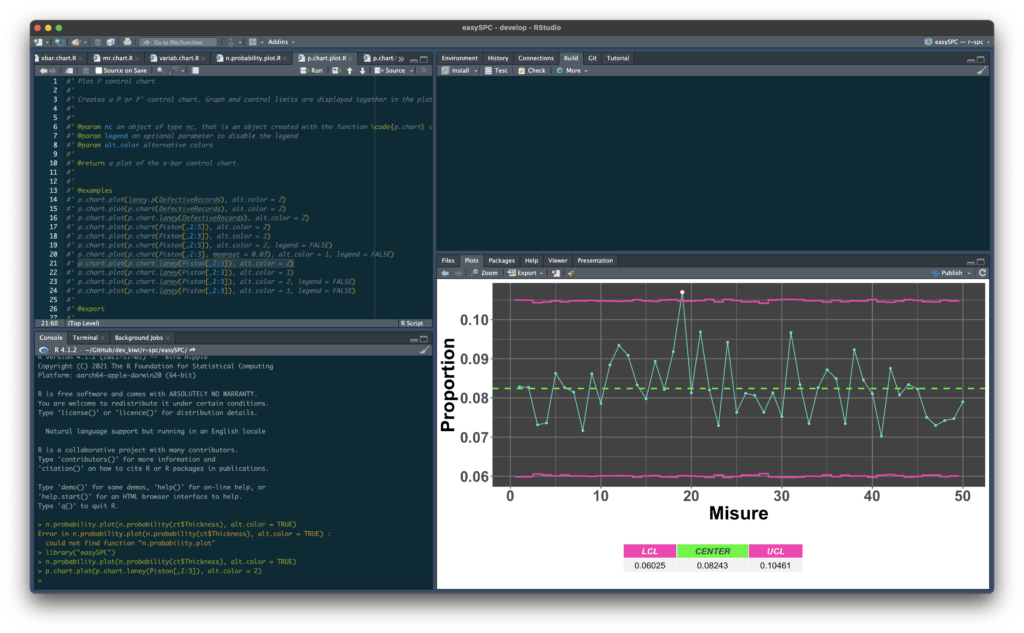
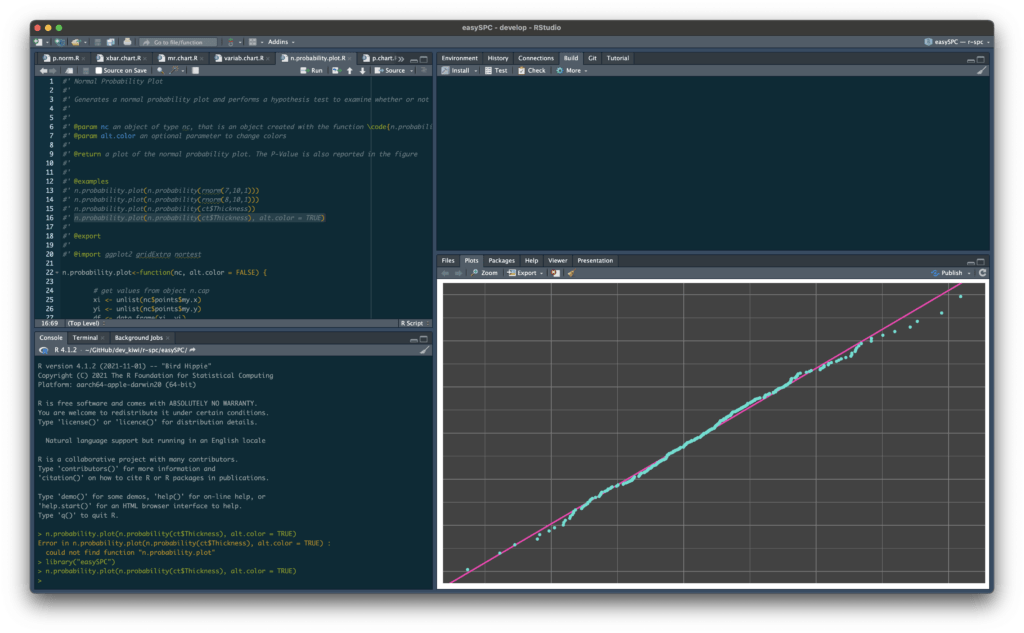
Training on the job
To elevate the capabilities of the analyst team, targeted industrial statistics courses were deemed essential. Kiwi stepped forward with its โtraining on the jobโ service, a compendium of theoretical and practical courses encompassing industrial statistics. Over the years, Kiwi has developed a diverse range of training programs spanning from statistical quality to experimental design. A substantial portion of the training is dedicated to exercises and practical applications. All topics are discussed through real-world case studies and examples, utilizing the statistical software Minitabยฎ.
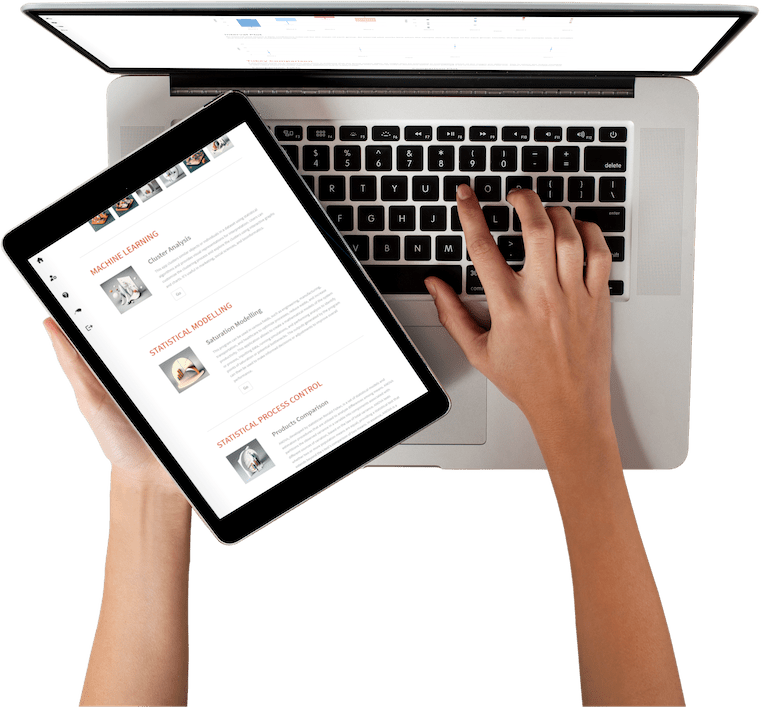
Course catalogue
Our four courses will enable you to make true data driven decisions based on solid factual evidence.
- Statistical Modeling
- Statistical Quality Analysis
- DoE: experimental design
- DoE advanced
The Results
In conclusion, the implementation of Statistical Process Control (SPC) has catalysed a remarkable enhancement in product quality, accompanied by a substantial reduction in variability across production processes. The timely identification and rectification of deviations have played a pivotal role in minimizing production waste. This dual outcome has not only solidified production consistency but has also optimized operational efficiency, empowering a more efficient utilization of company resources. SPC has emerged as a cornerstone in the transformative journey towards enhanced product quality and reduced operational waste.